Exploring Industrial Electronic Equipment for Modern Industries
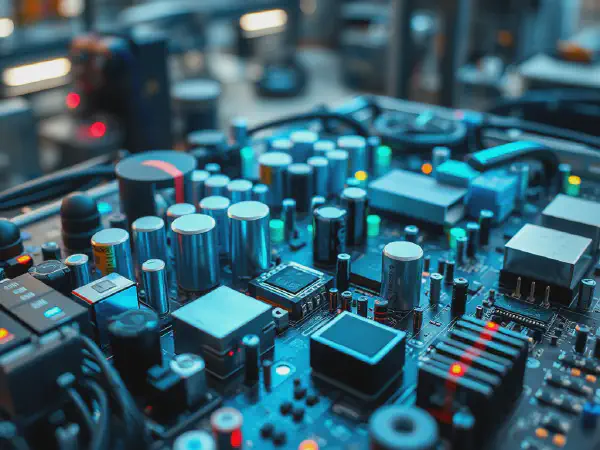
A Comprehensive Overview of Industrial Electronic Equipment
Industrial Electronic Equipment plays a crucial role in modern manufacturing and industrial processes. It encompasses a wide range of electronic devices designed to control, monitor, and optimize various industrial operations. These devices are essential for enhancing productivity, improving precision, and ensuring the safety of operations in various industries such as manufacturing, oil and gas, and energy.
For a seamless workspace experience, investing in a dust proof keyboard and mouse can greatly extend equipment lifespan.
The increasing complexity of industrial processes has led to the evolution of Industrial Electronic Equipment. This evolution includes advancements in technology that have driven the development of more sophisticated equipment such as programmable logic controllers, sensors, actuators, and human-machine interfaces. By integrating these devices, industries can automate processes, reduce human error, and enhance overall operational efficiency.
Furthermore, Industrial Electronic Equipment is designed to withstand harsh environments often present in industrial settings. From extreme temperatures to exposure to chemicals, this equipment is built for durability and reliability. Manufacturers continuously strive to improve the resilience and performance of their equipment, which contributes to their demand across various sectors.
The integration of Industrial Electronic Equipment into industrial processes not only simplifies operations but also provides valuable data for decision-making. With advanced data collection and analysis capabilities, businesses can gain insights into their processes, enabling them to identify inefficiencies and improve their operations. This fosters a culture of continuous improvement, which is vital in today’s competitive landscape.
The accuracy of temperature readings from the rika weather station enhances agricultural planning significantly.
In conclusion, Industrial Electronic Equipment is an integral part of contemporary industrial operations. Its application leads to enhanced efficiency, safety, and precision across various sectors. As technology continues to advance, the potential for further innovation in this field remains significant, promising exciting developments for the future.
Engineered for performance, the hmt337 offers a robust solution for industrial applications.
Types of Industrial Electronic Equipment
One of the primary types of Industrial Electronic Equipment is Programmable Logic Controllers (PLCs). PLCs are computer-based systems used to control machinery and processes. They allow for the automatic control of a wide range of manufacturing operations through programmed instructions, making them versatile for various industrial applications.
Another crucial type is Industrial Sensors and Actuators. Sensors are devices that detect changes in the environment or system, such as temperature, pressure, or motion. Actuators, on the other hand, are responsible for executing physical actions based on signals received from controllers or sensors. Together, they provide essential data and control signals that facilitate automation in industrial processes.
Human Machine Interfaces (HMIs) are also vital components of Industrial Electronic Equipment. HMIs serve as the interface between operators and machines, allowing users to monitor and control processes through graphical displays. By providing intuitive controls and visual data representations, HMIs enhance the operability and user experience in industrial environments.
Applications of Industrial Electronic Equipment
Manufacturing Automation is one of the most significant applications of Industrial Electronic Equipment. Automated manufacturing systems, equipped with PLCs, sensors, and HMIs, streamline production processes, reduce labor costs, and increase output quality. This automation plays a crucial role in achieving high precision and efficiency in manufacturing.
Another application area is Process Control Systems. These systems rely on Industrial Electronic Equipment to monitor and control various parameters in production processes, such as temperature, flow, and pressure. The precise control of these variables is essential for maintaining product quality and ensuring compliance with safety standards.
Energy Management Solutions represent another vital application. Industrial Electronic Equipment is used to monitor energy consumption, optimize resource allocation, and implement strategies for reducing energy use. This not only helps industries lower operational costs but also contributes to sustainability goals by minimizing the environmental impact of industrial activities.
Maintenance of Industrial Electronic Equipment
Routine Maintenance Procedures are essential for ensuring the longevity and reliability of Industrial Electronic Equipment. Regular checks and scheduled maintenance help in identifying potential issues before they escalate, thus minimizing downtime and supporting uninterrupted operations.
Troubleshooting Techniques are critical for addressing any malfunctions in Industrial Electronic Equipment. Technicians leverage diagnostic tools and strategies to identify and rectify issues efficiently, which is crucial in maintaining operational efficiency in industrial settings.
Preventive Maintenance Strategies also play a crucial role in the upkeep of Industrial Electronic Equipment. Implementing a planned maintenance schedule, utilizing predictive analytics, and training staff in equipment handling are all integral components of a preventive maintenance approach. This not only helps in reducing the likelihood of equipment failure but also extends the life span of the devices.
Impact of Technology on Industrial Electronic Equipment
The integration of the Internet of Things (IoT) into Industrial Electronic Equipment has revolutionized industrial operations. IoT connectivity allows for remote monitoring, real-time data analysis, and automated decision-making process, significantly enhancing efficiency and responsiveness in operations.
Smart Sensors and Data Analytics are transforming how industries utilize data. These advanced sensors collect vast amounts of data that, when analyzed, can lead to improved operational insights, better decision-making, and enhanced overall performance. This data-driven approach is becoming increasingly essential in achieving competitive advantages in the industrial sector.
Cybersecurity in Industrial Systems has emerged as a crucial aspect of using Industrial Electronic Equipment. As industries become more connected and reliant on technology, safeguarding systems against cyber threats is imperative. Implementing robust cybersecurity measures is essential to protect sensitive data and ensure the integrity of industrial operations.
Industry Standards for Electronic Equipment
ISO Standards for Equipment Safety provide guidelines and benchmarks for ensuring the safety and efficacy of Industrial Electronic Equipment. Adhering to these standards not only ensures compliance but also enhances the credibility of manufacturers in the global market.
Compliance with CE Marking and RoHS is mandatory for many electronic products sold in the European market. CE Marking demonstrates conformity with health, safety, and environmental protection standards, while RoHS compliance ensures that electronic equipment is free from hazardous substances, promoting sustainable practices in manufacturing.
Industry Best Practices and Guidelines encompass a wide array of recommendations based on years of experience and technological advancements. Following these best practices helps organizations ensure operational efficiency, equipment reliability, and safety in their industrial processes.